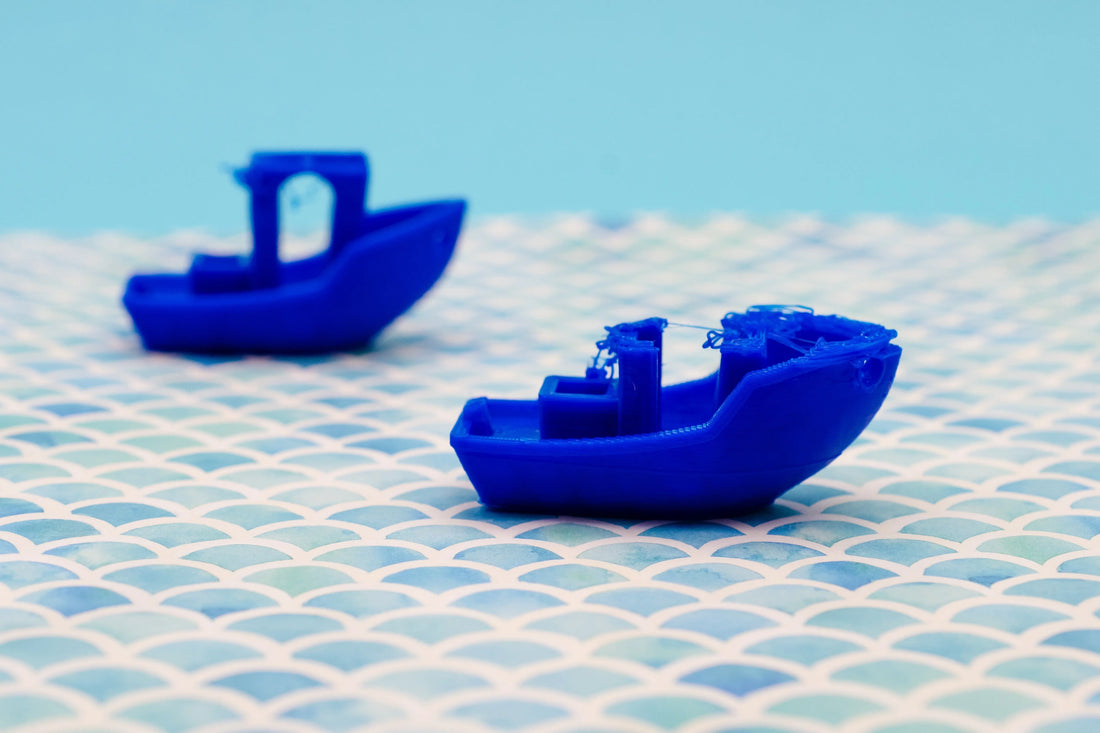
The Most Common 3D Printing Issues & Solutions
Mark SzymanskiShare
Photo by Megan Lee on Unsplash
The Most Common 3D Printing Issues & Solutions
3D printing is a great technology that is capable of incredible things. From complex geometries to easily producing finely-detailed parts, it can accomplish many things other manufacturing methods cannot. However, 3D printing isn't foolproof, and sometimes issues can crop up in your prints. Here are some of the most common problems that will come up when printing and how to solve them.
Bed Adhesion
The Problem
The first layer is by far the most important when 3D printing. If your first layer goes down well and is properly stuck to the bed, there's a very good chance the rest of your print will complete with no problems. That said, bed adhesion is likely one of the most common problems you'll experience and can be frustrating to troubleshoot. The classic "printing spaghetti" is usually the result of insufficient bed adhesion.
The Solution
One of the most common solutions is tuning first layer squish. Ensuring the first layer is properly laid down at the correct height is extremely important. There is an excellent guide out there for how to tune this first layer squish.
Another cause of poor bed adhesion is bed cleanliness. Even if your print bed looks clean, it may have invisible residue that has gathered on it, especially if you've touched the bed with your bare hands. This will leave oils from your skin on the bed which can negatively impact bed adhesion. A good habit to follow is:
- Clean your print bed with isopropyl alcohol between each print
- If you start to notice adhesion issues, clean with warm soapy water and then with isopropyl alcohol
- Avoid touching the print surface with your bare hands if possible
The size of the footprint of the part on the print bed can also affect adhesion. Parts that are very large or very small can experience issues. Very small parts don't have enough surface area to properly stick to the bed, and large parts can experience warping as the part cools, causing them to curl up off the bed. One solution in these cases is to add a brim to the part. This is extra material on the first layer that makes the footprint of the part larger without adding extra layers that will curl, improving bed adhesion. This brim is then removed after printing.
Depending on what material you're printing with, adding an enclosure can also help bed adhesion. Materials like ABS are very difficult to print without an enclosure. PETG can be printed without an enclosure, but it's often very helpful to use one.
Clogs
The Problem
Nozzle clogs are the bane of every 3D printing enthusiast. There are many things that can cause them, and many solutions, some more effective than others.
One cause of clogs is heat creep. This is when the filament gets too hot before it reaches the nozzle, which causes it to soften and expand outwards into the hotend, pressing against the inner walls and clogging up. If this happens, the first thing to check is that your temperature is set properly for the filament you're using. Running a filament too hot can cause heat creep. Next check if your extruder cooling fan is running properly.
There's another cause of heat creep that may not be something one would expect: printing too slowly. I discovered this one when I was trying to print a specific part and the nozzle kept jamming because of heat creep. The part was being printed in normal PLA with the same settings I've used for dozens of parts before. However, this part had a specific strange feature to it: a large section of it had supports underneath. The supports themselves weren't the problem, but the first layer on top of the supports was printing very slowly. When this happened, the filament wasn't being pushed out fast enough to avoid heat creeping up the length of the filament, causing the clogs. It puzzled me for weeks - hopefully this will prevent someone else from having the same frustration I did!
Another common cause of clogs is printing with a lower-temperature material after a higher-temperature one without fully purging the nozzle. This will cause the higher-temperature material to remain stuck in the nozzle, causing the clog.
The Solution
There are various ways to solve clogging problems. One of my personal favorites is the NoClogger. It's a specially designed tool that is used to push into a printer's extruder and down into the nozzle, forcing out any clogs that may be present.
Another option that requires some skill is performing a cold pull. The process is as follows:
- Use a relatively high temperature filament, PETG or Nylon would work great.
- Set the extruder to the temperature you would normally use for this filament.
- Push the filament through, purging some through the nozzle to ensure the filament is making contact with the entire inside of the nozzle.
- Turn off the extruder heat.
- This is the tricky part - once the temperature drops sufficiently that the filament is mostly solid but not stuck inside the nozzle, pull it out. Ideally the end of the filament you've removed will have taken the shape of the nozzle and removed all material from the nozzle, including any debris or stuck filament with it.
Stringing
The Problem
Another very common problem that is less catastrophic to your print than the others, but is still frustrating to deal with, is stringing. Stringing happens when the nozzle "travels" between two points but doesn't extrude any filament. Residual pressure inside the nozzle can cause a small amount of filament to "ooze" out, creating a thin string of filament between the two travel points.
This issue generally doesn't completely ruin prints, but it can be frustrating to clean up. Different filaments can display different stringing properties, so solving the problem requires tweaking a few different parameters.
The Solution
Choosing a different material can sometimes be an option. PETG tends to be stringier than PLA, for instance, so if your part doesn't require the benefits of PETG, you could choose a different material for printing.
As mentioned before, the root cause of stringing is that there's excess pressure built up in the hotend, causing filament to ooze out during travel moves. One way to solve stringing is to reduce this pressure by increasing retraction settings. A retraction setting between 0.5mm - 3mm is generally used for direct drive setups, and 5mm - 8mm for Bowden style extrusion setups. There are many stringing test prints that you can use to test what retraction values work best for your printer.
You can also adjust hotend temperature to reduce stringing. By reducing the hotend temperature, you can make the filament liquefy less and therefore tend to string less. Of course, reducing temperature has its limit as you can't reduce the temperature too far without compromising print quality and strength.
Conclusion
3D printing, like any manufacturing method, comes with its own share of challenges and obstacles to overcome that may prevent you from getting the parts you need.