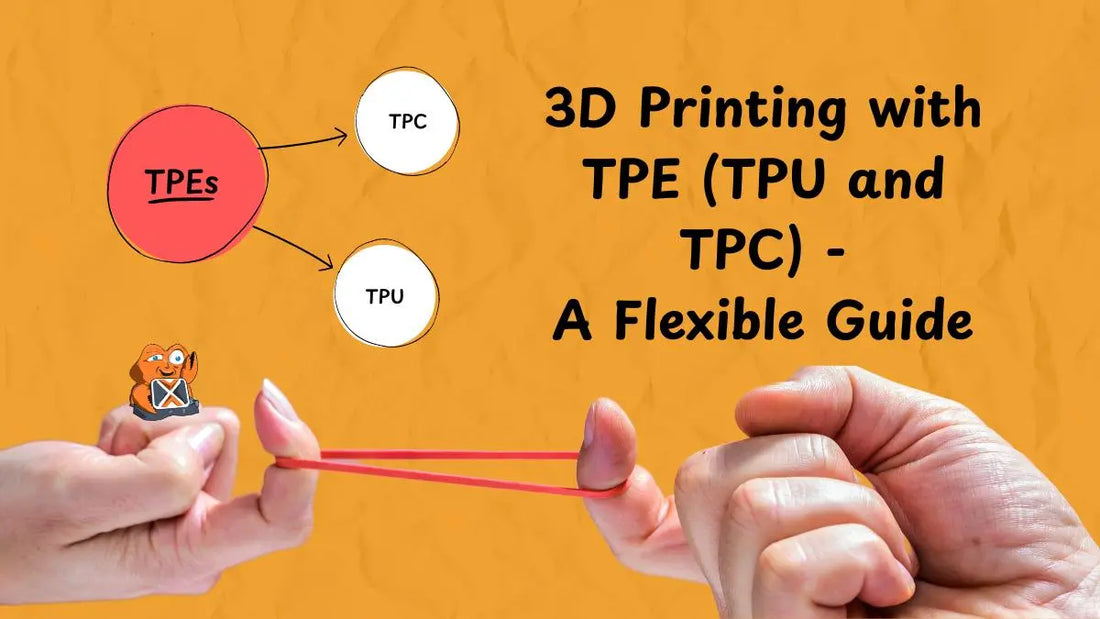
3D Printing with TPE (TPU and TPC)- A Flexible Guide
Todd LouthainShare
3D Printing with TPE (TPU and TPC)- A Flexible Guide
3D printing has revolutionized various industries, from manufacturing to prototyping. While traditional materials like PLA and ABS have been popular, flexible materials like TPE, which include TPU, and TPC, are gaining traction for their unique properties. These materials offer a wide range of applications, from soft toys and wearable devices to automotive components and medical devices.
Coex 3D produces several TPE filaments of varying durometers. These are broken down further into TPU and TPC’s. Each durometer option will have its unique characteristics and applications.
Understanding TPE (TPU and TPC)
TPE (Thermoplastic Elastomer):
TPEs are a blend of thermoplastic and elastomeric materials, offering both flexibility and durability. They are available in various hardnesses and can be customized to meet specific requirements. TPEs are commonly used for soft toys, shoe soles, gaskets, and medical devices.
- TPU (Thermoplastic Polyurethane):
- Properties: TPUs are known for their excellent abrasion resistance, flexibility, and tensile strength. They are often used in applications requiring high performance and durability.
- Applications: TPUs are popular for automotive components, sports equipment, footwear, and industrial parts.
- TPC (Thermoplastic Copolyester):
- Properties: TPCs are a type of polyester with enhanced flexibility and toughness. They offer good chemical resistance and dimensional stability.
- Applications: TPCs are used in automotive parts, medical devices, and consumer goods.
3D Printing with Flexible Materials
- Printer Compatibility: Not all 3D printers are compatible with flexible materials (TPEs). It's essential to check if your printer can handle the specific material properties and extrusion temperatures. Most importantly would be having a direct drive extruder.
- Slicer Settings: Adjust slicer settings like temperature, speed, and infill density to achieve optimal results. TPEs need to be printed slowly. Experimentation may be necessary to find the best settings for your material and project.
- Supports: When support is needed, using TPEs to support itself may require snipping or cutting to remove. This is due to the superb layer bonding.
- Post-Processing: Some flexible materials may benefit from post-processing techniques like annealing or boiling water to improve their properties or remove any residual support material.
Advantages of Using TPE, TPU, and TPC
- Flexibility and Elasticity: These materials offer excellent flexibility and elasticity, making them ideal for applications requiring soft or deformable components.
- Durability and Resilience: TPEs (TPUs and TPCs) are known for their durability and resilience, making them suitable for demanding environments.
- Chemical Resistance: Many of these materials exhibit good chemical resistance, making them suitable for applications exposed to various chemicals or harsh conditions.
- Biocompatibility: Some TPEs are biocompatible, making them suitable for medical devices and implants.
Conclusion
TPEs offer a versatile range of properties, making them a valuable 3D printing material. Just like any 3D printing material, quality matters. A higher-grade filament will yield a higher-grade print. By understanding their characteristics and adjusting printer settings accordingly, you can create functional and innovative products. Whether you are designing soft toys, wearable devices, or industrial components, these flexible materials provide endless possibilities for 3D printing applications.
If you have questions about this complex filament category, please don’t hesitate to contact support@coex3d for advice and answers.